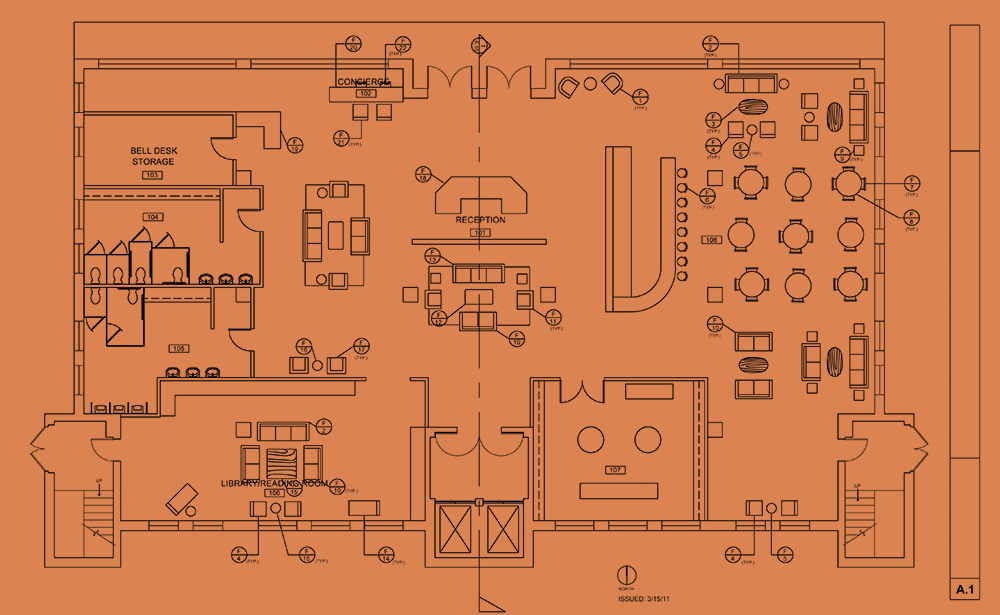
Lean Manufacturing I - Modifying Plant Layout
Caterpillar is the world’s largest manufacturer of medium and high-speed diesel engines, with ratings ranging around 13600hp. Caterpillar India Private Limited, Hosur, incorporated on 18 Oct '88, primarily manufactures diesel engines, generator sets ranging from 1800 KVA to 2275 KVA and parts thereof.
As part of the Lean Manufacturing Internship program, the group isolated the assembly line area to carry out research and improve the crane utilization. We went about this by capturing the value & non-value added time and thereby estimating the current efficiency.
The team comprised of Rengasamy, Pradeep Kumar, Tamil Arasu and Prasannah Jagannathan.
Objective:
To suggest modifications to the plant layout to improve the Return On Assets (ROA) for optimum asset utilization and improve worker safety.
Problem Isolation:
The existing mixed model incorporating underslung & jib cranes in the assembly area for part handling reduced the efficiency of the instruments.

Existing Work Distribution
The work distribution was uneven as Crane 1 comprised of 43% cumulative time (VA & NVA time) while Crane 2 & 3 had 32% and 25% of the cumulative time.
Calculations:
The estimated time comprising of the value added (VA), and non-value added (NVA) times gives the total time of crane utilization in workstations 1-9.
- Crane 1: Crane utilization time ∑t = 360 + 450 + 510 + 780 = 2100 sec (35 min) | For 6 engines (per shift) = ∑n * ∑t = 6 * 35 min = 210 min
- Crane 2: Crane utilization time ∑t = 190 + 455 + 530 + 320 = 1495 sec (25.5 min) | For 6 engines (per shift) = ∑n * ∑t = 6 * 25.5 min = 153 min
- Crane 3: Crane utilization time ∑t = 240s + 280s + 320s + 440s = s (21 min) | For 6 engines (per shift) = ∑n * ∑t = 6 * 21 min = 126 min

Time calculations are rounded off to the nearest tens.
From the above calculations, we can deduce the current workload that is pegged at 58.3% for crane 1 and 42.5% and 35% for cranes 2 & 3 respectively.
Optimization techniques:
- Work Balancing
- Continual Elimination
Work Balancing:
The cumulative crane utilization time in the mixed model assembly line is estimated at 489 min. The crane utilization time is unevenly distributed among the three cranes. To prevent over-utilization of the cranes beyond their optimum range, we have come up with the balanced workload time between the three cranes thereby spreading the workload among the three cranes effectively.

Spaghetti diagram tracing the revised movement of cranes in the workstation thus enabling work distribution.
Optimum crane utilization time as per historical usage patterns = 180 min approx.

Result:
Work balancing results in the efficient utilization of cranes. The distribution and balancing the workload among the three cranes result in optimised usage of crane resulting in a current efficiency of 50% approx. This model can be readily adopted with minimal alteration without loss of productivity and is, therefore, a useful short-term proposal.
Continual Elimination:
Under the continual elimination technique, we introduced a second jib crane in addition to jib crane 1 to replace the (underslung) cranes 2 & 3 thereby resulting in an optimized assembly line comprising of jib cranes 1 & 2. This new set up allows us to efficiently eliminate a whole crane and improve the current efficiency of the newly introduced crane system. We utilized AutoCAD to build the blueprint of the plant layout and visualize the positioning of the jib crane in the modified screen.

Modified plant layout utilizing AutoCAD
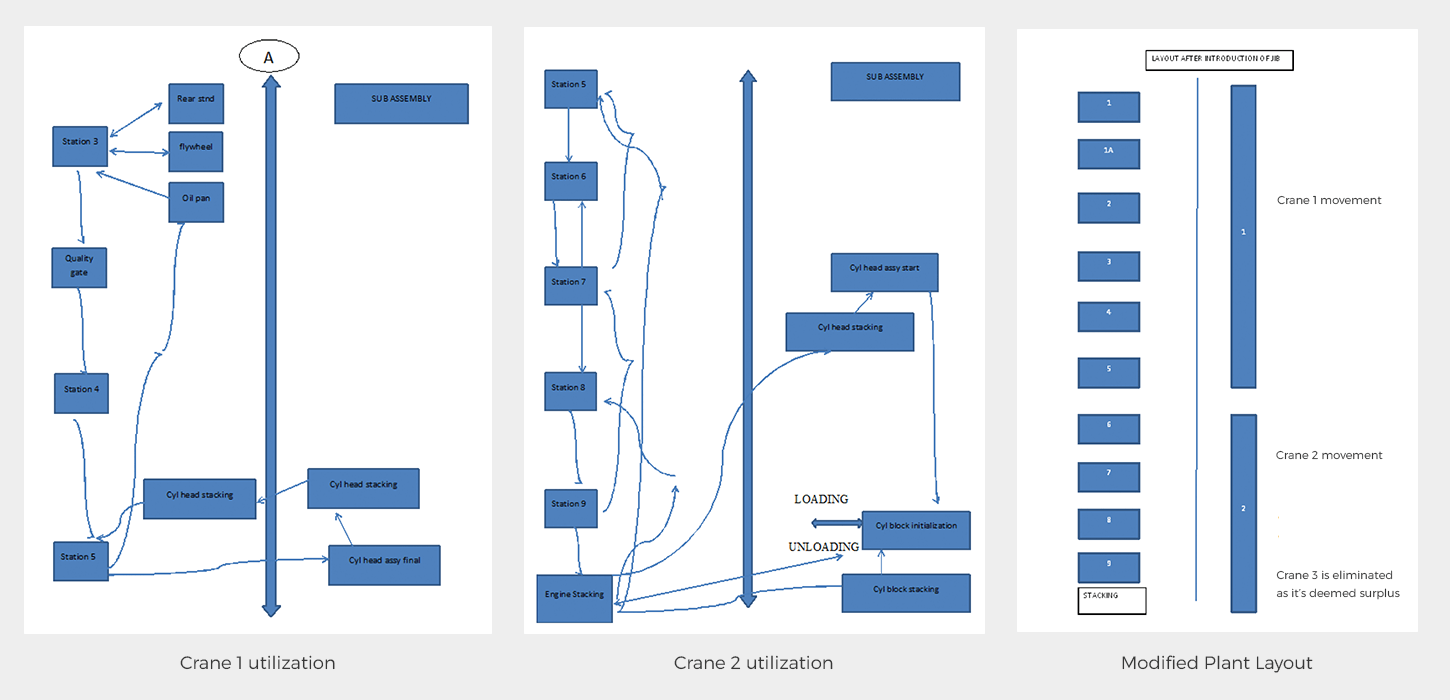
Spaghetti diagram tracing the revised movement of jib cranes 1 & 2 in the workstation.
Result:
Continual elimination results in the efficient utilization of the overall crane system. With the introduction of an additional Jib crane, we can carry out the entirety of operations using jib cranes 1 & 2, efficiently eliminating the underslung mechanism. The adoption of this suggestive model is time inducing and results in loss of productivity and is therefore rightly deemed as a long-term proposal.