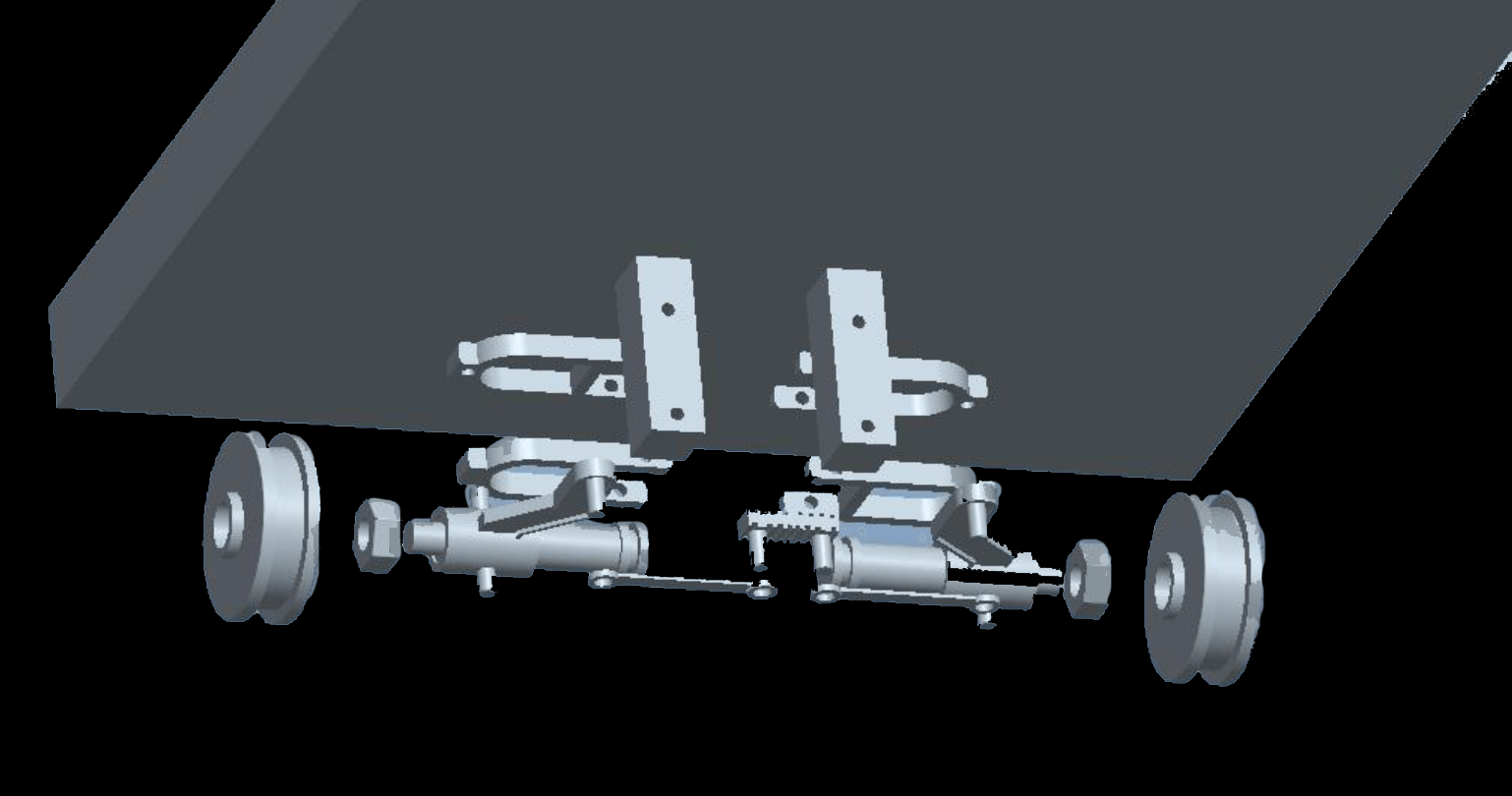
Lean Manufacturing II - Monorail Hybrid Ackermann System
Caterpillar is the world’s largest manufacturer of medium and high-speed diesel engines, with ratings ranging around 13600hp. Caterpillar India Private Limited, Hosur, incorporated on 18 Oct '88, primarily manufactures diesel engines, generator sets ranging from 1800 KVA to 2275 KVA and parts thereof.
As part of the Lean Manufacturing Internship, the group was led to address the congested workflow and traffic across the workstations by the introduction of a monorail system to transfer the engine block from assembly line to testing.
The factory setting entails well-planned strategies that have clear economic value. Instead, we wanted to bring the spirit of a lab to the factory: We collaborated with the in-plant manager and the workers, directly prototyping and trying out ideas on the machines that are used for production. The aim was to bring prototyping closer to production in the ideation phase and by definition, make the prototypes production-ready.
Objective:
To address the congested workflow and traffic across the workstations by introducing a monorail trolley system from stations 4 to 9 and further to the stacking area. This plan exempts stations 1 to 3 (Please refer final layout) as a change in setup results in mounting spatial and equipment constraints.

Ackermann Flat Deck Trolley:
- Initially, flat deck trolley is chosen because of its capacity to carry heavy loads (as engine blocks weigh around 2800kg).
- The Ackerman steer is suitable because of the need to turn the heavily loaded trolley into sharp corners without much difficulty.
- It also works to balance the lack of space available within the workspace.

(Reverse) Ackermann Model:
The team utilized Pro E to design the 3D structure of the steering.
We designed a reverse Ackermann geometry to compensate for the significant difference in slip angle between the inner and outer front tires while cornering. The geometry helps reduce pressure on the wheels with negligible constrain on low-speed maneuvers. The handle that is used to move the trolley is connected to a drag link of the rear wheel assembly employing a connector that passes the longitudinal movement of the handle to the drag link. The drag link further transfers the handle movement to the wheels by turning it to the desired proportion by dragging the link accordingly. Thus by using the Ackermann steering type, the trolley can be used in fine corner’s with ease despite the heavy load.
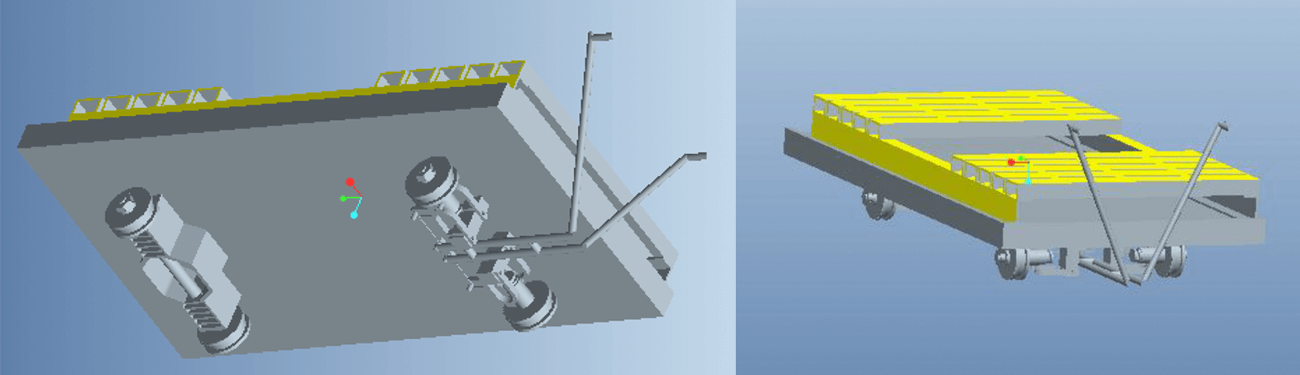
Figure 1.2 Final Assembly with palette on top
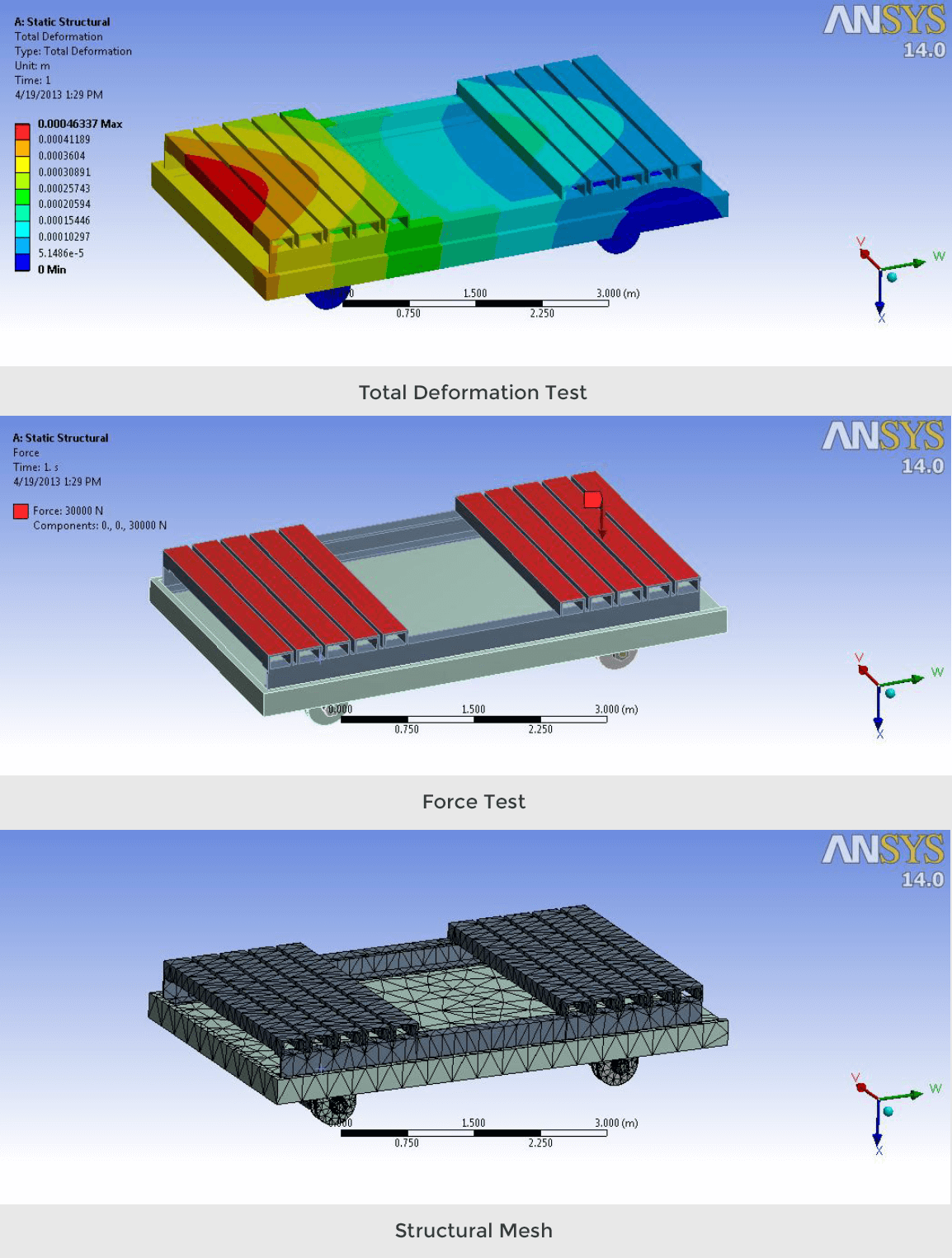
Stress, Force & Deformation Test
Utilized ANSYS to test the structural composite of the Ackermann setup with the palette on top. Maximum deformation is concentrated on the static front axle that is fortified with additional meshing (refer Fig. 1.2). The force test and structure indicate a robust design.
Scope for consideration could be improved by incorporating an actual engine setup (with accurate weight and dimensions) for prototyping.
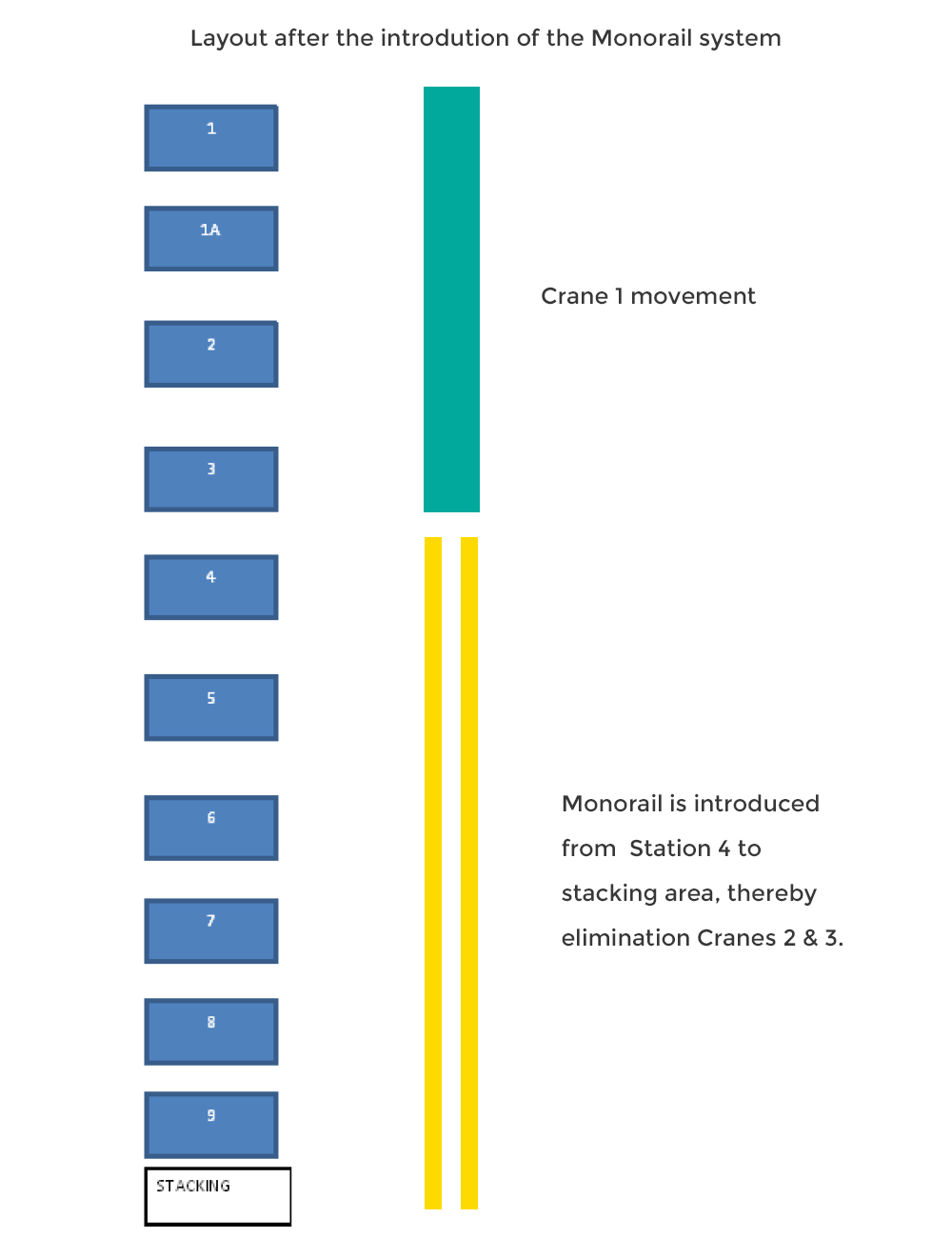
Monorail Trolley System results in:
- Due to spatial and equipment constraints, the monorail set up does not extend to Stations 1 to 3.
- The Ackermann steering system enables the manual movements of heavy loads in the range of 2800kg.
- The new setup results in an organized workflow with worker ergonomics depicting an F1 pit stop crew.